High-temperature gas-to-gas heat exchangers are commonly found within sulfuric acid plants, functioning as interchangers or preheaters for the catalyst bed, and as preheaters at the sulfur furnace.
These recuperators see very high temperatures and high-temperature differentials. Typically, at least one, if not both gas streams are highly corrosive if allowed to condense. Home Air Exchanger

If a standard shell and tube design is employed, several failure modes will most likely occur. These include:
Cold-end corrosion – The cold gas stream often enters the heat exchanger at a temperature below the dew point of the constituents contained in the hot gas stream. This creates a potential for material surface temperatures below that dewpoint. These are commonly referred to as cold spots. If a gas stream is in contact with a cold spot, condensation will occur. The resulting acid will cause localized corrosion commonly referred to as cold-end corrosion.
Cold-end fouling – When an SO3 rich gas stream is present, cold spots will cause the SO3 to precipitate. The SO3 creates a tenacious bond with the metal tube wall. These deposits continue to build up and if the unit is not shut down for maintenance, the resulting blockage of the gas stream will lead to obvious capacity issues.
Stress failures – High-temperature gas-to-gas recuperators experience rapid and extreme temperature changes. This results in rapid and significant material expansion and contraction. With standard shell and tube designs, the tubes will most likely expand at different rates due to uneven temperature distribution within the tube bundle. This results in uneven forces exerted on the tubesheet by the tubes and ultimately failure of the tubesheet welds.
Unanticipated pressure drop - If the pressure drop is higher than anticipated, the operational flow rate will be less than anticipated as well.
All of these failure modes impede the performance of the recuperator and ultimately the performance of the entire plant. Once in operation, the remedy or repair is very costly and time-consuming. If not remedied, the operational life could be as short as several years.
It is imperative to thoroughly evaluate the intended application and design the recuperator with those operational demands and the above failure modes in mind. The issues need to be addressed during the design phase so that reliability and efficiency can be designed into the recuperator.
A thorough analysis of the unit is essential to address cold spots, uneven stresses, and pressure drop before the unit is manufactured so that costly adjustments and repairs are avoided and overall operating life and productivity is maximized.
Given experience and expertise, the solution is straightforward. The goal is to create thermal symmetry within the unit. The following features help achieve that goal:
Variable pitch tube bundle – The pitch, or distance between tubes, varies between rows. This will allow more even flow distribution throughout the tube bundle and will lead to uniform temperature across the tubesheet. This also contributes to a lower pressure drop and higher thermal efficiency.
Unique baffle arrangements – Unlike standard shell and tube arrangements, inlet locations and baffle arrangements resulting in a combination of cross flow and parallel flow in addition to the common counterflow are all utilized. Multiple passes are incorporated which allows circuiting the cold gas inlet stream away from the existing hot gas stream, thereby avoiding cold spots where they would be problematic. The arrangement further assists with temperature uniformity.
Full annular inlet plenums – Plenums allow the gas streams to enter the recuperator at lower velocity promoting uniformity and further avoiding cold spots. This design also avoids isolated areas of higher pressure drop common at connections and furthers the unit’s efficiency.
Designing with CFD and FEA analysis
Computational fluid dynamics (CFD) and finite element analysis (FEA) are at the core of the thorough evaluation that is required to verify pressure drop, heat transfer rates, temperatures, and flow though the recuperator. Experience provides the starting point when determining tube pitches, and baffle and plenum arrangement. The design is adjusted based on initial analysis until they are proven by subsequent runs. This analysis is the difference between a five-year operating life and a 20+ year operating life.
CFD and FEA programs have become more powerful throughout the years and are capable of analyzing very large models with a very fine mesh. They can analyze heat transfer models that are very sensitive and difficult to converge. However, this takes considerable computer time, which is not always possible when a rough budgetary price is needed for a project in the initial stages of design work.
There are techniques to simplify this modeling which involve focusing on areas of most concern. Experience tells us that these are typically in low-temperature regions, since these are most frequently the location of failures.
The analysis of this area of interest involves a very complicated array of surfaces including the gas flow on the interior and exterior of the tube and a detailed model of the tube wall itself. Completing this anaylsis for every tube across the bundle is very time-consuming and cumbersome.
In order to provide initial/budgetary sizing and arrangements, a simplified approach is needed for an initial screening. For this initial screening, assumptions can be made for the gas flows based on a standard boundary layer and convective heat transfer coefficients. Assumptions can also be made to model the tubes as a single surface.
With a simplified model, an analysis of the “area of interest” can be completed relatively quickly to confirm the suspicion of cold spot potential in that region.
The recuperator design can then be modified and reanalyzed. With the simplified model, it is practical to run several iterations to zero in on the most advantageous arrangement.
Based on the findings from the initial analysis of the “area of interest”, the tube pitch is modified to allow more uniform flow on the shell side and more uniformity across the tube sheet. The air inlet is relocated further up the shell to coincide with warmer tube wall temperatures. Then, the baffle arrangement is adjusted to accommodate this unique inlet location.
The baffles will first guide the air in a co-current arrangement, running parallel to the hot gas. This is followed by a section of crossflow, with the remainder of the flow being directed in a counter flow to the hot gas in the tubes. The baffles are also evaluated to minimize pressure drop.
It would be remiss not to mention several other considerations in this discussion that have a significant impact on the operating life of the recuperator.
Flanged and flued expansion joints are designed and located along the shell to alleviate stresses due to thermal expansion. The expansion joints are pre-compressed during installation so that they will operate near normal at the elevated temperatures experienced during operation.
The maximum operating temperature as well as the gas composition needs to be considered during material selection. The highest metal temperature, as determined through the CFD analysis, and the stream composition are the main criteria used in the determination of materials. Material and fabrication costs, availability, and desired operating life are part of the equation as well. Experience and expertise are the best tools when determining the material that minimizes cost and maximizes operating life.
As with any heat exchanger design, the potential for vibration should be reviewed. Small adjustments in the baffle arrangement and nozzle configurations can eliminate vibration concerns and are easily addressed during the design phase. If ignored, vibration can be very costly to address in the field.
Depending on the configuration of the recuperator, how often it will cycle, and how rapid and extreme the temperatures increase, a floating tubesheet might be recommended. A floating tubesheet would absorb the additional stresses caused by these conditions and further eliminate the concern of weld failures.
Engineering out issues during the design phase is the key to success
In conclusion, addressing the potential for cold-end corrosion and fouling, minimizing uneven stresses, and evaluating pressure drop during the design phase is crucial to long-term cost savings and maximum operating life. This is best accomplished with experience aided by CFD and FEA analysis. With this attention to detail in the design phase, the result will be a recuperator with a 20+ year operating life.
Connecting people in business and industry with one another for the betterment of all. Become a BIC Alliance Member today.
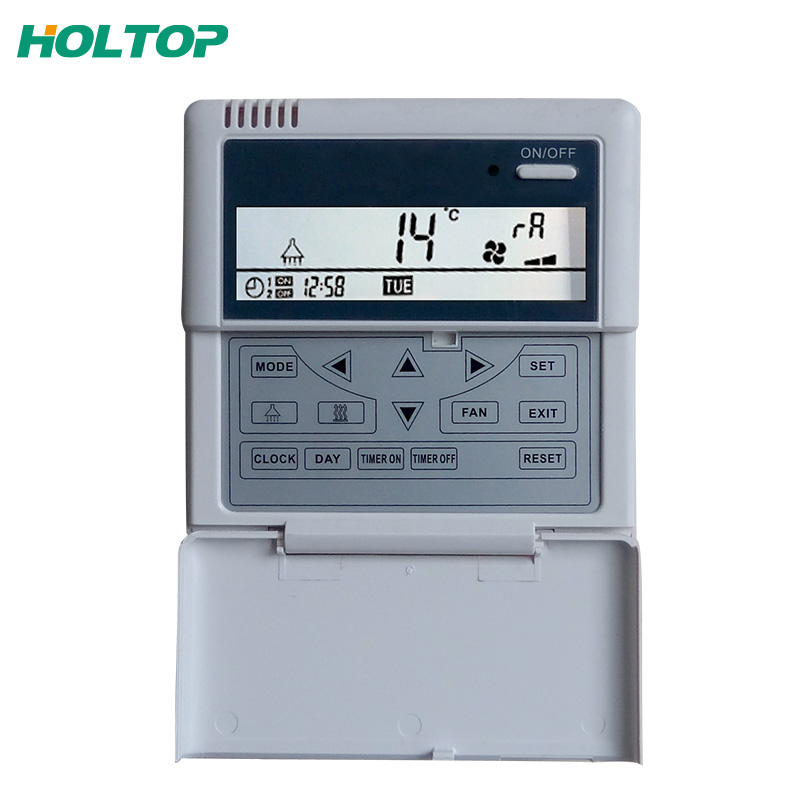
Horizontal Air Handler Copyright © 2023 BIC Alliance, Inc. All rights reserved.